Over the last decade, 3D printing has grown from a niche technology used primarily by hobbyists and engineers to a transformative manufacturing process that is changing the face of many industries, including the automotive sector. In recent years, 3D printing has been used to create parts for trucks, including Volvo Trucks fixtures and older Daimler Unimogs. The technology has allowed manufacturers to create parts that can't be easily produced using traditional manufacturing methods, making it easier and more cost-effective to produce spare parts and custom components.
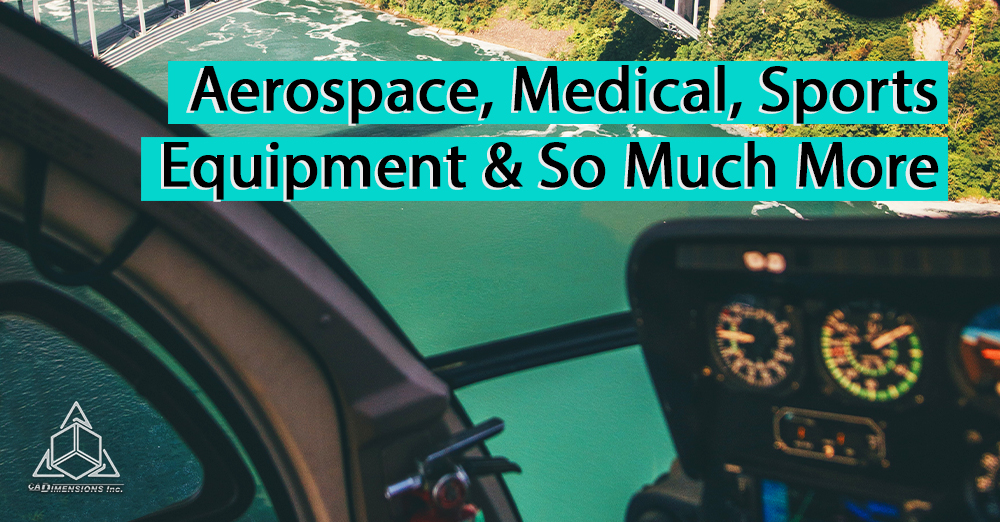
Yancheng Terbon Auto Parts Co., Ltd., a leading supplier of brake and clutch parts, is one of the companies that has embraced 3D printing for truck parts. Established in 1988, the company produces a wide range of brake and clutch parts, including brake pads, brake shoes, brake discs, brake drums, clutch discs, clutch covers, and clutch release bearings. By using 3D printing technology, Terbon has been able to expand its production capabilities and offer a wider range of products to its customers.
One of the advantages of 3D printing is that it allows manufacturers to create complex shapes and geometries that would be difficult or impossible to produce using traditional manufacturing methods. This means that 3D printing can be used to create a wide range of parts, from small components to large assemblies. In the case of truck parts, 3D printing can be used to create replacement parts for older vehicles that may no longer be in production, or for custom components that need to fit specific applications.
Another advantage of 3D printing is that it allows manufacturers to produce parts on demand, rather than having to maintain large inventories of spare parts. This can reduce lead times and inventory costs, while also allowing manufacturers to offer a wider range of products to their customers. For example, Terbon can use 3D printing to produce brake pads and clutch discs in small quantities, rather than having to order large batches from a supplier.
In addition to creating spare parts, 3D printing can also be used to produce prototypes and tooling. This can allow manufacturers to test and refine designs before committing to full-scale production, reducing the risk of expensive mistakes. For example, Terbon could use 3D printing to create a prototype of a new brake pad design, test it on a vehicle, and refine the design as necessary before putting it into full production.
However, there are also some challenges associated with 3D printing truck parts. One of the main challenges is ensuring that the parts meet the required standards for strength and durability. While 3D printing can produce parts with complex geometries, it can be difficult to ensure that the parts are strong enough to withstand the stresses of real-world use. This is particularly important for parts such as brake pads and clutch discs, which are critical components that must be able to perform reliably under all conditions.
Another challenge is the cost of 3D printing technology. While the cost of 3D printing has decreased in recent years, it is still more expensive than traditional manufacturing methods for high-volume production runs. This means that 3D printing is best suited for low-volume and custom production runs, rather than large-scale mass production.
Despite these challenges, 3D printing has a bright future in the automotive sector, particularly in the production of truck parts. As the technology continues to improve and costs continue to come down, we can expect to see more and more companies like Terbon using 3D printing to create spare parts, custom components, and prototypes. This will allow manufacturers to offer a wider range of products to their customers, reduce lead times and inventory costs, and improve the quality and reliability of their products.